Castinox: a steel company with quality and safety guarantees
Castinox is aware that quality products are essential for the Company to properly operate and move forward, so it has established its management policy based on the following points:
Castinox’s organisation is engaged with meeting requirements and permanently improving the quality management system’s efficacy, bearing in mind the needs and expectations of interested parties, analysis of the organisational context and the strategic direction defined.
Castinox deems Quality, understood as customer satisfaction, to be one of its basic principles for action.
Occupational Hazard Prevention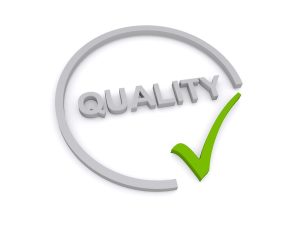
Castinox has established an occupational hazard prevention policy, defined in the following points:
- To establish prevention as a priority objective, in order to minimise harm and prevent the deterioration of health for all members of the Organisation.
- To apply the Occupational Health and Safety management system, meeting legal requirements and constantly ensuring that applicable regulations are enforced.
- To require that provides and subcontracted companies fulfil corresponding safety and health guidelines, when working at Castinox’s facilities.
Environment
Castinox has established the environmental policy to be followed, defined in the points below:
- Application of an Environmental Management system, following the criteria established in governing legislation applicable in this regard.
- Contribution to sustainability and improving environmental impact.
- Considering environmental factors in planning and developing new manufacturing processes.
- Communication with providers to apply requirements from the Environmental Management system.
- Priority use of natural resources, obtaining the greatest power savings possible, as well as rational use of all of them.
We have Management Policies aimed at permanent improvement
We are aware of how important a good management system is, a system that engages the company with the human team and with the quality we offer to our clients. Castinox is a stainless steel company involved with permanently improving both our production processes and internal management, which allows us to invest in perfecting the technical assessment we offer and the quality of our parts. Quality certificates back us up, and our production level is proof of our progress over more than 20 years of experience held by this steel company.
Our Permanent Improvement commitment arises from this policy, which details objectives, goals and programmes to be carried out. Castinox Management leads, encourages and maintains this policy, providing human and material resources to guarantee that this Policy is met, offering training and/or awareness for our own staff and third parties, promoting participation and responsibility and keeping a commitment to transparent communication. This Policy is reviewed and kept updated, declared as compulsory and duly communicated to all interested parties.
At Castinox, we want to offer a quality production system with guarantees. This is why, since 1999, we have held the certification ISO 9001:2008, which includes Castinox’s production processes. We have procedures for each one of them, from order or project reception until shipping to the client.
Our company has a culture of permanent improvement, which uses client feedback and measurement and study of our own internal indicators as tools to improve. Our commitment to quality was awarded and proven by our production volume since the very beginnings of our activity, which has only grown over the course of the more than twenty years of Castinox’s experience.
We have qualified technical personnel, specialised in adapting feeder systems and parts filling. If the client requests, we also provide assessment in manufacturing the models.
The company has software to calculate and simulate the casting process. With this software, we are able to predict the metal’s behaviour during the filling and solidification process. In this way, we decrease the risks of defects appearing in the parts, thereby increasing quality and productivity for our products and services.
At Castinox, we want the end quality as required by our clients. This is why we have a department in charge of verifying that the product meets expectations. We have a team and the resources necessary to perform some of the required trials, and subcontract the rest to duly-approved local companies. At Castinox, we offer:
- Chemical analysis
- Non-destructive trials (penetrating liquids, magnetic particles, ultrasounds, radiographies…)
- Destructive trials (traction, metallography, corrosion, resilience…)
- Dimensional control
Trials are conducted with duly-calibrated equipment, as per different standards (ASME, EN, DIN, AFNOR, UNE, BS, etc.) with entities certified by ENAC.
One of our fundamental features and the key to our success is the short delivery time and our processes control. Thanks to constant investments made in equipment and new facilities, we can offer short delivery times to our clients. We strictly plan and control each one of the processes involved in manufacturing the parts, such as:
- Sanding Control
- Moulding
- Fusion
The main purpose of preventative maintenance is to prevent incidents and to thereby improve quality for our entire service. Total daily testing takes place, on all equipment and processes, with a technological programme we own and software by Omron. This is how we minimise the time it takes us to locate any breakdown to the maximum, and we can resolve it with no need to stop the manufacturing process, all while being able to modify any parameter without interrupting operation of the machinery in question.
On the other hand, we also have a Scada programme to visualise the equipment in real time and generate consumption statistics. With the support of our own work equipment, at Castinox we seek to cover requirements stemming from business growth. We have already achieved proven optimisation for the machinery by means of total automation, thereby reducing electrical failure by 90% and mechanical breakdowns by 50%.